
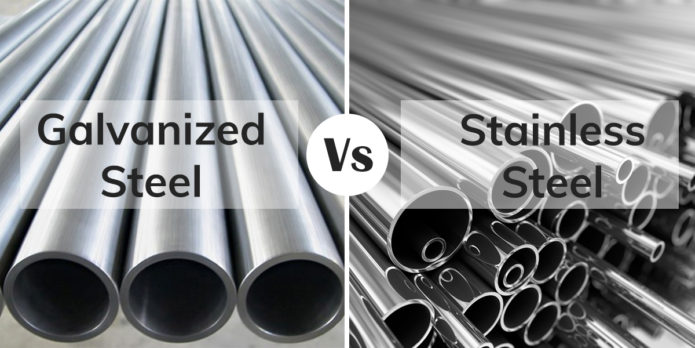
Grade 316 has better corrosion resistance than grade 304 in many chemicals as well as in marine atmospheres.

The corrosion resistance is improved by an addition of 2 to 3% of molybdenum, as well as 18% chromium and 10% nickel. Stainless Steel 316, or Grade 316, is known as the marine alloy. The physical properties and thermal treatments are similar to those of grade 304. Parts made from this grade are generally limited to service at temperatures up to 425✬.

Grade 304L is used in parts of 4mm and thicker which will be welded but not post weld annealed. Sensitisation can allow intergranular corrosion to occur. 304Lģ04L Grade 304L is a low carbon (<0.030%) variant of 304 with the same corrosion resistance, but with less susceptibility to sensitisation when welded at thicknesses of 4 mm or greater, or after heat treatment. It is suitable for use in a variety of applications, in fact it is the most common stainless steel, and about 60% of all stainless steel used in the world is grade 304. It is sometimes known as 18/8 stainless steel, since it contains 18% chromium and 8% nickel. This grage has excellent workability, weldability and impact strength. 304ģ04 Grade 304 is the most widely used stainless steel with good resistance to atmospheric corrosion and to many organic and inorganic chemicals. Austenitic stainless steels are non-magnetic in the annealed condition, but will become slightly magnetic when cold worked. Welding of this stainless steel grade is straightforward, although welding procedures are a little different to those used for carbon steel. Strength can be increased by cold working, but not by heat treatment. Austenitic stainless steels are usually used in the annealed condition, when they have a useful range of mechanical and physical properties. The most common extra element is molybdenum, which greatly improves corrosion resistance. They contain 17 to 25% chromium and 8 to 20% nickel, and may contain other elements to achieve the desired properties. Austenitic Grades of Stainless SteelĪustenitic stainless steels are easy to work and weld, and have excellent ductility, toughness and corrosion resistance with good strength. Each group has different dominant characteristics, and there are several grades within each group. The stainless steels can be divided into five groups – austenitic, ferritic, duplex, martensitic and precipitation hardening. Although straightforward for most applications, choosing the optimum grade of stainless steel can sometimes be complex, and Austral Wright Metals engineers and metallurgists will be pleased to provide assistance. There are many different stainless steels, with different amounts of alloying elements added to give the best balance of corrosion resistance, mechanical properties and cost. It is this passive layer that gives stainless steel its corrosion resistance. If it is damaged, the film usually heals spontaneously. This film is called the passive layer and forms rapidly in ordinary atmospheres. Chromium reacts strongly with oxygen to form a very thin, invisible, stable oxide film on the surface of the stainless steel. Stainless steels are steel alloys that contain more than 10.5% chromium with excellent corrosion resistance.
